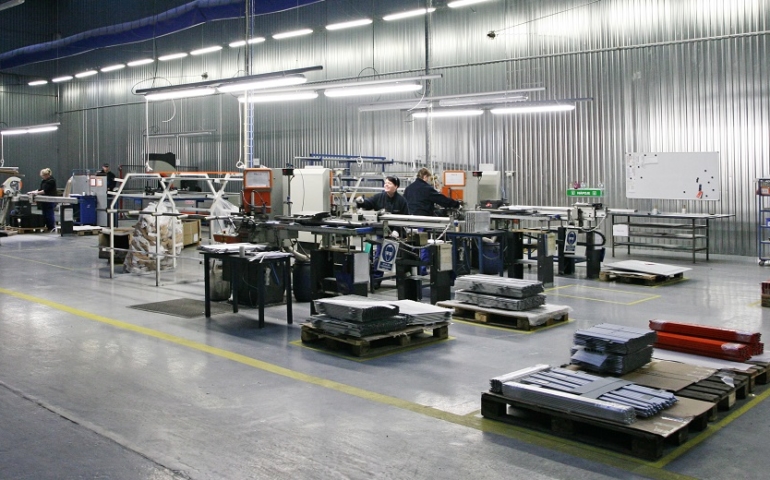
Showdown Displays Europe, s.r.o.
Rozhovor s Vítem Zajíčkem – jednatelem společnosti Jansen Display
Velké příběhy vznikají i z maličkostí. Z drobných, nenápadných částeček, které se časem samy začnou spojovat a nabalovat jako velká sněhová koule.
Přejít k obsahu | Přejít k hlavnímu menu
Rozhovor
12. prosince 2020
Společnost BENEŠ a LÁT a.s. se svou slévárnou nesmazatelně zapsala do historie Průhonic, kde působila od 30. let 20. století. Po roce 2000 se postupně přestěhovala do čtyř nových závodů ve Středočeském a Libereckém kraji.
„I když se každý ze závodů věnuje odlišným technologiím pro zpracování neželezných kovů a plastů, všechny je spojují stejné hodnoty – úcta k tradicím, rodinná atmosféra, týmový přístup, ale i společný jazyk, kterým je v pojetí řízení společnosti informační systém“, říká Jan Lát a dodává: „Vedle tradičních technologií jsme našli zálibu i v objevování nových obzorů, proto jsme se vydali cestou výzkumu v oblastech 3D tisku kovů a souvisejících oborech. Stali jsme se spoluzakladateli společnosti CARDAM s.r.o., či jedním ze zakládajících členů Národního centra kompetence MATCA. Oba tyto subjekty se věnují matematickým simulacím, technologiím 3D tisku, problematice využití plazmatu a dalším odvětvím. Spoluprací v těchto uskupeních jsme se naučili optimalizovat design našich výrobků a zákazníkovi v našich matematických modelech představíme takový návrh, který ušetří materiál při zachování potřebné mechanické vlastnosti výrobku“.
Příběh naší společnosti je příběhem 20. století. Původní fabriku založil v roce 1934 pan Beneš v Praze – Holešovicích, dnešní Jateční ulice, ve vnitrobloku jednoho domu. Tam odléval například řeznické háky, nebo formy na šunky. Výrobu rychle rozvíjel a ve vnitrobloku už to dál nešlo. Těsně před druhou světovou válkou koupil v Průhonicích, což bylo tenkrát kus za Prahou, od místního sedláka pozemek. Tam založil slévárnu a zaměstnával pracovníky z nejbližšího okolí Průhonic, Hole, Rozkoše, Újezdu a dalších vesnic. Pak přišla druhá světová válka.
Slévárna byla preferovaným průmyslem i za války – vyráběly se výrobky pro třetí říši, tak jako ve všech továrnách, které směly fungovat v protektorátu. Pro mnoho lidí to byla jediná možnost přežití. Paní Benešová uměla perfektně německy a dokázala si na velitelství SS vyjednat, aby slévárna mohla nabírat a zaměstnávat lidi z Průhonic a okolí, namísto aby byli odesláni na nucené práce do Německa. Tím zachránila spoustě rodinám mámu, tátu, vlastně celou existenci. Z paní Benešové se stal takový malý lokální Schindler.
Paní Benešová zůstala sama se dvěma malými kluky ve věku jeden a tři roky a s fabrikou, která zaměstnávala sto lidí. Dala inzerát do novin, že hledá někoho, kdo podnik dál povede. Přihlásil se můj děda, Josef Lát. Byl tehdy šéfem vývoje sléváren ČKD v Praze. Protože byl vlastně najatý manažer, a ne vlastník továrny, nemusel po nástupu komunistů k moci z podniku odejít. A to i přesto, že se z najatého manažera stal i manžel – paní Benešová se stala paní Látovou, to vysvětluje i dnešní jméno společnosti. Fabriku vedl a řídil až do své smrti v roce 1980, což bylo naprosto unikátní.
Po dědově smrti to šlo s fabrikou od desíti k pěti. Po čtyřech letech přišli za naším tátou, který pracoval jako mechanizátor v nedalekém zemědělském družstvu, aby šel slévárnu řídit. Do podniku v roce 1984 skutečně nastoupil. Byl to fantastický vizionář. V té době jsme dělali hodně takzvaného speciálního programu, tedy dodávek pro zbrojní průmysl. Vyráběli jsme vstřikovací čerpadla do bojových vozidel pěchoty. Šlo o velké a těžké odlitky, které se ořezávaly na pásových pilách. Byla to těžká a pomalá práce. Táta se zamiloval do technologie řezání vodním paprskem. Byl první ve východní Evropě, kdo tento stroj dostal za železnou oponu. Věřil, že by mohl odřezávat vtoky odlitků automaticky.
Když táta zjistil, co vše se s ním dá dělat, tak u nás neskončil jako výrobní zařízení, ale jako laboratorní pracoviště, na kterém se vyvíjely aplikace pro další výrobce. A ty jsme pak dodávali jako hotová pracoviště třeba do Vagonky Studénka, pro Moser. To bylo fantasticky placené.
Přesně tak. Kupovali jsme roboty Nokia, Kuka, pumpy FLOW Systems a u nás se z toho stavěla pracoviště na klíč. Takže fabrika v roce 1989 končila s 23 miliony korun hotovosti na účtech. To by v dnešních penězích bylo více než čtvrt miliardy. Jenže v květnu 1990 táta musel jako „stará struktura“ z fabriky odejít. Během necelých dvou let se fabrika ocitla na hraně samotné existence. Byla cíleně „škrcena“ a připravována na privatizaci do rukou zahraničního konkurenta, pro kterého se už tehdy odlévalo pár výrobků.
Zahraniční investor podal privatizační projekt, ale táta se s tím nehodlal smířit. Připravil konkurenční privatizační projekt se svými dvěma bratry a v roce 1992 jsme si fabriku koupili do vlastních rukou. Dostal na to úvěr od banky, protože v restituci babička dostala zpět jen zlomek hodnoty podniku. Vzal si čtyřletý úvěr 42 milionů korun s úrokovou mírou 22 procent ročně. To by dnes zlomilo vaz kterékoli strojírenské firmě v Evropě. My jsme úvěr zaplatili do posledního haléře včetně úroků ve sjednané splatnosti.
Prakticky ano. Slévárna byla téměř bez práce. Významnější zakázky v té době byly jen od konkurenční společnosti se zájmem o privatizaci. Ta samozřejmě veškerou práci stáhla v okamžiku, kdy v privatizaci neuspěla. Díky tátovým kontaktům v oboru z let, kdy průhonický závod řídil, se podařilo obnovit spolupráci a výroba se zase rozjela.
Změn proběhlo mnoho. Od toho, že jsme se z původně jednoho závodu v Průhonicích rozrostli do čtyř závodů po republice; přes to, že jsme rozšířili portfolio technologií a zpracovávaných materiálů; až po rozvoj dalších kompetencí, jako je vývoj software pro řízení výroby, či vstup do odvětví aditivních technologií.
Ale popořadě. V závěru devadesátých let bylo čím dál těžší fungovat v Průhonicích. Hledali jsme proto nové místo. Od Fondu národního majetku jsme koupili zkrachovalou textilku ve Slané u Semil a v roce 2005 jsme tam odstěhovali z Průhonic první část výroby – vysokotlakou slévárnu Zn slitin. Díky fungování na Semilsku jsme objevili krachující pozůstatek Kovozávodů Semily – jejich vstřikovnu plastů jsme převzali týž rok v zimě těsně před bankrotem. Velmi nás oslovovaly synergie odlévání kovů a lisování plastů.
Během pár let jsme opět narazili na kapacitu průhonického areálu, a tak jsme hledali, kam odstěhovat i zbývající výrobu. Vybrali jsme starou betonárku v Poříčanech. V průběhu roku 2007 jsme od různých vlastníků odkoupili pozemky a chystali se na stavbu.
První komplikace stavby přišla už na podzim 2007, kdy nečekaně zemřel táta, pár týdnů po tom, co oslavil šedesátiny. Ten vůči bankám vystupoval jako záruka, že firma všechny závazky vždy uhradí – banky braly jeho slovo jako jistotu, garanci. V době jeho skonu se projednávaly úvěry na novou fabriku. Mně bylo v té době 25, sestře 33 a bratrovi 35 let. Fabrika měla obrat půl miliardy korun. Financující banka v nás okamžitě ztratila důvěru a jednání se komplikovala…
Absence majoritního akcionáře a „záruky“ z pohledu bank skutečně leccos komplikovalo. Naštěstí každý z nás sourozenců máme jiné vzdělání, a tak jsme každý mohl přispět tomu, abychom situaci překonali. Sestra je právničkou, a tak se ujala řešení všech otázek spojených s průběhem dědictví. Nechali jsme ji ustanovit správcem dědictví, aby společnost mohla dál fungovat do doby projednání dědictví. Bratr se věnoval obchodním otázkám, abychom měli zajištěné zakázky a vedle organizačních změn se nemuseli potýkat ještě s nějakým propadem zakázek. Vzhledem k tomu, že jsem v té době studoval VŠE a měl jsem zkušenosti z nákupu, padlo rozhodnutí, že finanční otázky budu řešit já. Hned v listopadu jsem se pustil i do výběru banky a v únoru 2008 jsme si vybrali a probíhal proces schvalování kompletního refinancování.
Pak přišla další „rána“ – vybraná banka v posledním schvalování nedostala souhlas s financováním od své zahraniční matky. V tu chvíli již byl objednaný materiál na stavbu nového areálu v hodnotě přes 30 milionů Kč.
Oslovili jsme tak druhou banku v pořadí. Díky tomu, že tato banka v Česku právě budovala korporátní klientelu a našemu projektu věřila, poskytla nakonec kompletní financování včetně přefinancování všech dosavadních úvěrů, a to navíc v neuvěřitelném termínu 5 týdnů od zahájení jednání. Stavba začala v květnu 2008 a 27.5.2009 jsme již spouštěli úplnou výrobu a měli kompletně přestěhováno z Průhonic.
Paradoxně nám krize napomohla – první signály přicházející krize jsme zaznamenali na podzim 2008 a reagovali jsme na ně hned v počátku. Když pak dopadla začátkem roku 2009 plnou vahou, již jsme měli velmi zeštíhlenou produkci. Navíc jsme potřebovali stěhovat výrobu a pokles poptávky nám to umožnil – strojní kapacity nebyly využité, a tak jsme mohli v tomto období stěhovat, aniž bychom ohrozili naše dodávky. Navíc díky dlouhodobé strategii diverzifikovat dodávky do různých segmentů průmyslu se dopad krize nedostavil v jedné drtivé vlně, ale v mnoha menších vlnkách, které se vzájemně vykrývaly. V celkovém pohledu propadl obrat o téměř 30 %, nicméně neznamenalo to žádné zásadní komplikace. Na konci krize – pro nás již v létě 2009 – jsme tak byli nachystaní s novými kapacitami, v novém závodě a mohli jsme tak naskočit na první vzestupnou vlnu.
Od roku 2009 se ekonomice v našem oboru dařilo poměrně pěkně růst dlouhých 9 let, během kterých jsme samozřejmě prožívali různé turbulence, ať už v podobě odlivu některých zakázek do Asie, nebo naopak strmého růstu výroby v letech 2016–2018. Každopádně až na podzim 2019 jsme pocítili korekci, na kterou počátkem letošního roku bohužel navázala koronavirová opatření.
Vidíte, vlastně jsem ještě nevysvětlil 4. závod z úvodu… V roce 2013 se nám naskytla příležitost rozšířit výrobní portfolio o další technologii lití hliníku – vysokotlaké přesné odlévání. Od německé skupiny TTS jsme převzali původní českou strojírenskou společnost Polak v Mimoni – shodou okolností původně, ve 30. letech, sídlila pár bloků od pana Beneše v Holešovicích. Tím jsme doplnili 3. výrobní závod v Libereckém kraji a celkově 4.
Vedle rozšíření portfolia tradičních technologií jsme se ale rozhodli dívat se i do budoucna a sledovat technologie, které slévárenství doplňují, nebo dokonce možná jednou nahradí. Tak jsme se začali věnovat oblasti aditivních technologií – 3D tisku. Ne však tomu, který si většina lidí představí – nevěnujeme se 3D tisku plastů, ale zůstáváme věrni kovům – ruku v ruce šly aktivity pořízení vývojové laboratoře 3D tisku včetně high-end tiskárny, na které dokážeme tisknout hliník, ocel, titan, inconel, či měď. Ve stejné době jsme společně s Fyzikálním ústavem Akademie věd ČR a Českou zbrojovkou začali připravovat vznik společnosti, která se bude věnovat aditivu a s ním souvisejícím matematickým simulacím, optimalizacím produktů a výrobních postupů a v roce 2016 tak vzniklo pracoviště CARDAM s.r.o.
V oblasti aditivu se dál rozvíjíme – stali jsme se jedním ze zakládajících členů konsorcia Národní centrum kompetence MATCA, které se věnuje oblasti 3D tisku a technologiím a jevům v oblasti plazmatu na vědecké úrovni. V konsorciu jsou sdruženy jak vědecké instituce, tak univerzity i průmyslové podniky – dnes má 16 členů.
Díky pochopení možností 3D tisku jsme se například naučili dělat topologickou optimalizaci výrobků. Takže můžeme zákazníkovi říct, že u jeho výrobku má v některých částech zbytečně moc materiálu a díky matematickým modelům mu umíme připravit návrh tak, aby ušetřil (materiál, zdroje…) a odlitek měl pořád ty správné mechanické vlastnosti. To zákazníci velmi oceňují. Ve slévárenské technologii dokážeme snáze opravovat jádra ocelových forem pro odlévání. Když se část formy poškodí, tak ji můžeme odbrousit a 3D tiskem ji vyrobit znovu. V těchto 3D tištěných částech můžeme mít chladící okruhy, které bychom do nich jinak nedostali. To je vhodné například pro odlitky, které musí mít lesklé povrchy, tvarové části jejich forem proto vyrábíme 3D tiskem. V rámci vývoje tiskneme také díly, „odlitky“, které se jinak vyrobit nedají, ale zde jsme spíš v oblasti prototypingu než sériového nahrazení tradičního slévárenství.
Polomaska je zajímavým příběhem – vlastně díky dlouhodobé spolupráci s akademickou sférou jsme včas zaznamenali výzvu od ČVUT, že hledají partnera, který by jim pomohl dostat jejich 3D tištěnou polomasku do podmínek sériové výroby, přišlo nám to jako přesně pro nás. Náš kolega, konstruktér, se vydal do ČVUT probrat s tamními vývojáři, jak si to představují, co bychom pro ně mohli udělat.
A vyplynula z toho spolupráce, která zpočátku byla čistě jen o designových úpravách produktu, aby byl vhodný pro sériovou výrobu, ale velmi rychle se rozvinula dál. Kolegové z ČVUT hledali i partnera, který jim pomůže se zastřešením výroby. To si vzal na starost CARDAM, věnoval se celému projektu včetně spolupráce s dalšími společnostmi, které zajišťují subdodávky některých dílů. Zároveň i výroba/kompletace už běžela pod hlavičkou CARDAMu. My jsme v tom řetízku nakonec jako jeden ze subdodavatelů, u kterého probíhá výroba části celé polomasky a část montáží. Polomaska se kompletuje z více prvků vyráběných v několika společnostech v České republice. Třeba finální montáž probíhá v České zbrojovce a v BENEŠ a LÁT, u nás ještě lisujeme skořepinu masky, další komponenty se vyrábějí v jiných společnostech napříč celou republikou. Je to krásný „konglomerát“ společností, které se do toho zapojily.
V celém vývoji a přípravě jich bylo dohromady 50. Takže super hnutí, které se dokázalo zformovat během pár dnů. Celá příprava byla neuvěřitelný fofr – ČVUT vyhlásilo v polovině března možnost zapojit se. Ještě ten den odpoledne za nimi vyrazil kolega. A na Velikonoční pondělí už jsme vyráběli první skořepiny. Takže od prvního setkání po sériovou výrobu uběhl přesně měsíc.
Standardní proces při vývoji dílu pro komerční sféru by vypadal tak, že bychom se dva až tři měsíce dohadovali o tom, než se usadí design. Pak by se vybírala nástrojárna, která by řekla, že na výrobu potřebuje 8 až 10 týdnů. Takže jsme na čtyřech až pěti měsících, což je i dnes bráno jako velmi slušná doba pro design-to-market. Jenže tady designér produktu našel konstruktéra, který mu během dnů řekl, jak by se dal sériově vyrobit. K tomu se přidala společnost, která výrobu zaštítila. Takže to, obrazně řečeno, na začátku byla dohoda tří lidí, kteří dokázali pružně reagovat. Už dva měsíce od první schůzky bylo 20 tisíc masek hotových.
Stavebnice nám přišly do cesty vlastně náhodou. Když jsme v roce 2005 přebírali sutický závod Kovozávodů Semily, tehdy již fungující pod značkou VISTA, zjistili jsme, že ve výrobním portfoliu jsou i stavebnice a hračky. Neváhali jsme a stavebnice jsme se rozhodli zachránit – vyrostli jsme na nich a byli jsme, a to se nezměnilo dodnes, přesvědčeni, že právě stavebnice podporují zručnost, představivost a technický zájem u dětí.
Vzhledem k celkové finanční situaci závodu v Suticích byly i stavebnice dlouhodobě podfinancované.
Abychom mohli pracovat na zlepšení jejich prodejnosti, bylo nutné věnovat se nejprve rozvoji, inovaci a zatraktivnění. Během patnácti let se stavebnice proměnila významně víc než za pětadvacet let před naším převzetím. Nejprve jsme věnovali ročně několik milionů korun tomu, abychom sanovali ztrátu ze stavebnic a hraček. Můžete to chápat jako nerozumné, ale my se na to dívali jako na filantropii, jako na investici do budoucích generací. V roce 2018 stavebnice poprvé nevygenerovaly ztrátu, ale skončili jsme v mírně kladných číslech, kde se od té doby držíme.
Díky inovacím, novým tvarům a prvkům se možnosti významně rozšířily. Na druhou stranu jsem přesvědčený, že i před třiceti lety jsme ze SEVY dokázali postavit vlastně cokoliv – protože hnacím motorem byla naše dětská představivost… Dnes SEVA dětem umožňuje vyrobit svůj sen realističtěji, ale zásadní ingrediencí stále zůstává fantazie, která je dětem vlastní. V posledních letech jsme se vydali cestou rozdělení nabídky SEVY do několika řad, jako je Rodina, Stavíme, Vesmír, Zvířata a podobně. Jak názvy napovídají, je dnes SEVA připravená pro stavbu domů, družic, raket, lunochodů, chaloupek, kočárků, zvířátek… Čehokoliv, co si umí děti představit a chtějí realizovat.
Abychom dětskou představivost a rozvoj dále podporovali, záměrně do SEVY nedáváme detailní „krokové plány“, které by děti jen slepě opakovaly, raději dáme pár fotek jako inspiraci – ať si každý tvoří to, na co má chuť. A že nám na našem Facebooku často přistanou kreace, nad kterými žasneme!
Zajímavá otázka… Nejsem sociolog, ale myslím si, že retro vlny jsou přirozené – je to asi generační projev, kdy si mladí rodiče plní své sny. Kupují dětem to, co sami měli rádi, s čím si hráli, po čem toužili… Nevnímám to jako něco novodobého. Stejně jako se opakují módní styly, tak si myslím, že se přirozeně vrací i kvalitní produkty. To, že produkt přežije generace, vypovídá právě o jeho kvalitách než o tom, že ho rodiče svým dětem vnucují. Monti System se v posledních letech navíc stává sběratelskou záležitostí, má vlastní fankluby, kde si zpravidla tatínci vyměňují zkušenosti, dotváří jednotlivá autíčka do podoby věrných kopií konkrétních aut a podobně.
Určitě – snažíme se podporovat všestrannost. Nabízíme hračky od jednoho roku, aby si děti mohly trénovat první úchopy, první skládání – sem patří třeba Blok. Další level jsou velké Mozaiky – včelí úl, kde se skládají obrazce ze šestiúhelníků, následuje SEVA, od základní až po SEVU elektro, kde jsou převody a ovládání. Pro kreativitu je tu třeba Seko nebo Mosaic. Vědomosti podporujeme deskovými hrami, jako je Ukaž! Co víš?, a to zase ve verzích od nejmenších, až po školáky… Chceme, aby naše stavebnice rozvíjely děti v moha směrech, inspirovaly a dávaly možnost tvořit.
Jsme českou rodinnou firmou. Jsme hrdí na to, že můžeme navazovat na dlouhou rodinnou tradici české výroby. Je pro nás důležité, že naše produkty vznikají v Česku díky umu českých lidí, že dávají zaměstnání a živobytí rodinám, které tu budou vychovávat další generace. Ano, přesun do Asie by velmi pravděpodobně přinesl větší zisky nám, ale mnoha lidem by sebral práci i motivaci… Tento pohled máme k celému našemu podnikání. Jsme přesvědčeni, že v Česku je mnoho chytrých a šikovných lidí a jsme rádi, že i my můžeme pomoci českému hospodářství se posouvat. Kromě toho, že stavebnice v Česku vyrábíme, snažíme se pokrýt i materiály a ostatní vstupy od českých výrobců. Vedle podpory vlastní ekonomiky je to i hledisko zdravotní a ekologické – známe dobře své dodavatele, můžeme se na jejich kvalitu vždy spolehnout a nevznikají zbytečné přesuny na dlouhé vzdálenosti, které by způsobovaly zbytečnou zátěž pro přírodu.
S výrobci se věnujeme i snížení ekologické stopy materiálů jako takových – loni jsme uvedli na trh velmi úspěšnou verzi stavebnice Blok z melásky, zlepšujeme obalové materiály, zmenšujeme obaly, aby se nevozil „vzduch“. Je toho hodně, co může každý za sebe udělat pro to, aby se nám tu dobře žilo.
Fotografie poskytla společnost
BENEŠ a LÁT a.s.
Sdílet na sociálních sítích
Kontaktujte nás. Rádi zodpovíme všechny vaše dotazy, předložíme vám nezávaznou cenovou nabídku.
Showdown Displays Europe, s.r.o.
Velké příběhy vznikají i z maličkostí. Z drobných, nenápadných částeček, které se časem samy začnou spojovat a nabalovat jako velká sněhová koule.
Z STUDIO, spol. s r.o.
Narodil se v roce 1969 ve Zlíně, kde v současné době žije i pracuje. Vystudoval ČVUT v Praze, obor Technická kybernetika. V roce 1995 založil společnost Z STUDIO, spol. s r. o., která se věnuje komplexní péči o reklamní, firemní a technické tiskoviny.
GEMINI oční klinika a.s.
Služeb očního chirurga Pavla Stodůlky využili Tomáš Baťa junior nebo prezident Václav Klaus. Všechno ale přebíjí zákroky, kdy navrací pacientům zrak. "Na začátku své kariéry jsem se na takovou věc neodvážil pomyslet. Ani jako na krásně vymalovaný sen," říká Stodůlka.